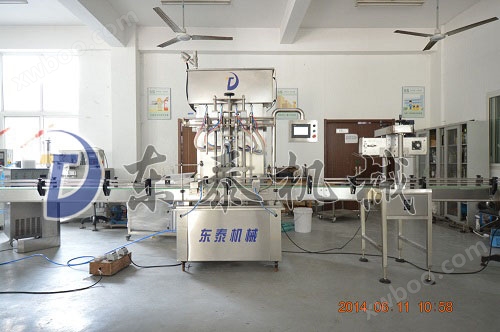
Product Name: Four Head Fully Automatic Edible Oil Filling Line
Product model: ZLDG-4 series
Product Introduction:
This filling machine is a four head fully automatic quantitative filling machine for oil liquids, suitable for filling various viscous liquids such as lubricating oil, edible oil, etc. This filling machine has achieved the transition from single sales to providing fully automated unmanned equipment, replacing manual labor.
Scope of application:
This series of oil filling machines is widely used for filling various oils and viscous liquids, such as peanut oil, blended oil, sunflower seed oil, rapeseed oil and other edible oils.
Technical parameters:
Filling speed: 500-1000 barrels per hour
Filling capacity: 1-6 liters/0.1-1 liters (can be customized according to user requirements)
Filling accuracy: ±≤0.5%FS
Working power supply: 220/380V
Working pressure: 0.5-0.7Mpa
Number of filling heads: four
Detail drawing of four head fully automatic edible oil filling line:


Principle characteristics:
1. This edible oil filling machine is a fully automatic quantitative liquid filling machine, suitable for filling various oils such as lubricating oil and edible oil.
2. This model is equipped with a touch screen display, a variable frequency speed control conveyor belt of 8 meters, an automatic induction type capping machine, and a vacuum anti drip device.
3. The filling machine has the characteristics of beautiful appearance, high filling accuracy, convenient adjustment, and easy operation.
Technical features:
1. Suitable for filling liquids such as fruit juice, seasonings, cosmetics, detergents, pesticides, pharmaceutical products, petroleum products, etc.
2. The main motor and bottle conveyor belt both adopt variable frequency speed regulation, which is easy to operate.
3. The ultrasonic liquid level control system is used to effectively control the liquid level in the cylinder, making the filling process smoother and more accurate.
4. Automatic bottle supply detection system: detects whether bottles are delivered to the conveyor belt and automatically starts or stops (optional for customers)
5. During the filling process, the valve nozzle can always be kept equidistant from the liquid level. The filling can also be designed with the valve nozzle inserted or removed from the liquid according to the type of bottle and material liquid, effectively avoiding the phenomenon of liquid foaming.
6. Automatically monitor whether there are bottles under each filling valve, and automatically control the opening of the filling valve to avoid the loss of filling materials due to filling without bottles.
7. Use equipment and materials that comply with GMP hygiene standards;
8. The chassis and other components are made of 304 # corrosion-resistant stainless steel, which is easy to clean and meets GMP standards. Widely used in enterprises such as food, medicine, cosmetics, etc.
The best selling point of the device:
1. Human computer interface, directly set the filling volume;
2. PLC program control, frequency converter speed regulation linear filling;
3. High precision volumetric flowmeter, with accurate and reliable quantitative measurement;
4. Mechanical seal and vacuum suction double anti drip leakage;
5. Fast first and then slow dual flow efficient filling.
Four head fully automatic edible oil filling line case:


Maintenance work for filling machines is essential:
1. Before going to work every day, observe the moisture filter and oil mist filter of the pneumatic combination two-piece. If there is too much water accumulation, it should be removed in a timely manner. If the oil level is not enough, it should be refilled in a timely manner;
2. During production, it is necessary to regularly inspect and observe mechanical components to see if they are rotating and lifting normally, if there are any abnormalities, and if screws are loose;
3. Regularly check the grounding wire of the equipment and ensure reliable contact; Regularly clean the weighing platform; Check if there is any air leakage in the pneumatic pipeline and if the air pipe is broken;